HAPTIC TELEROBOTICS: APPLICATION TO ASSISTIVE TECHNOLOGY FOR CHILDREN WITH DISABILITIES
Nooshin Jafari1, Kim Adams1, Mahdi Tavakoli2
1Faculty of Rehabilitation Medicine, University of Alberta, Canada
2Electrical & Computer Engineering Department, University of Alberta, Canada
ABSTRACT
Robotic systems for master-slave teleoperation with haptic feedback capability have been used in diverse areas such as surgical simulation and telerehabilitation. Such systems have not yet been used by children with disabilities who can potentially control the master human-machine interface to sense and manipulate objects using the slave robot. This paper presents a comparison of candidate robots for the roles of the master robot as the child’s human-machine interface and the slave robot for object manipulation in the environment. After establishing the appropriate robot choice, the control parameters for the stable system are determined. The system will subsequently be used for studies with children with disabilities doing manipulation tasks such as haptically guided drawing and painting in virtual and physical environments.
BACKGROUND
The word haptics has its roots in the Greek words “haptesthai and haptikos” meaning “to touch” (ISO, 2011), and comprises touch (tactile/cutaneous) and kinesthetic (force) perceptions. A haptic interface has been defined as being concerned with the “association of gesture to touch and kinesthesia to provide for communication between the humans and machines” (Hayward et al, 2004, p.16). Haptic interfaces have been used in different areas including robot-assisted surgery and surgical training (Tavakoli et al., 2006) and telerehabilitation (Atashzar et al., 2012).
To date, few studies have exploited the functional benefits of haptic teleoperation systems for children with disabilities. Studies have investigated the performance of non-impaired adults on maneuvering a virtually simulated wheelchair (e.g., (Crespo & Reinkensmeyer, 2008)), motion impaired adults on human-computer interaction (e.g., (Langdon et al., 2000)), adults with Down syndrome performing cutting and painting (Covarrubias et al., 2014), and adults with visual impairments controlling computer cursors (e.g., (Sjöström, 2001)) Studies with children with disabilities involve only toddler power wheelchair users to help their maneuvering skills (a child with severe motor impairment (Crespo et al., 2010) and a child with spina bifida (Chen et al., 2011)).
Our research aims primarily at using haptic assistive technology for enabling access to object play and manipulation (e.g., playing with objects, drawing and painting) which ultimately will lead to overall task performance improvement and higher percentage of successfully finishing the task. With increased opportunities for such activities, it is possible that children with disabilities experience improved cognitive development thanks to object manipulation (e.g., in the context of play (Gibson, 1988) and education (Minogue & Jones, 2006)). The feasibility of haptic assistive technology systems has remained unexplored in manipulation and exploratory tasks for children with disabilities.
Purpose
We propose to use a haptic telerobotic system featuring position error based (PEB) control in a master-slave configuration. The child’s interface will be the master robot, which sends position commands to the slave robot and receives forces if the slave robot is in contact with an object in the environment. The force feedback will be proportional to the difference between the position of the master and slave robots, which serves as the commanded position for the slave robot. This paper presents a comparison of candidates for the roles of master robot for the child interface and slave robot for manipulating or exploring objects in the environment. After establishing appropriate robot choice, the control parameters for a stable system are determined.
materialS
FEATURES COMPARISON
We established our comparison criteria based on several features of serial and parallel robots. The Falcon is a parallel robot, and though the Premium has a parallel linkage designed to reduce its inertia (Lee, 2010), the robot can be approximated as a serial-chain robot. Candidate features were positional accuracy (the robot’s positional deflection from its desired location), kinematic design (related to the possibility to easily map DOF of the master and the slave), workspace, and inertia. In theory, parallel robots are recognized with higher positional accuracy and smaller inertia while serial robots are recognized with simpler kinematic design and larger workspace (Wavering, 1999), (Pandilov & Dukovski, 2014). However, these generalizations may not apply to all robots taking into account each robot’s individual structure. Some of these exceptions are discussed later.
In master-slave teleoperations, the choice of the master and slave robots is very much application-dependent. Our first step is to develop a telerobotic system for children with disabilities who have a small range of motion, but want to do manipulation tasks such as drawing and painting. This implies features including safety, ease of use, and smaller apparent inertia for the master and operational workspace, and positional accuracy for the slave.
Our intention is to have the master held by the child. This necessitates the master being very safe. The Falcon robot has a smaller workspace than the Premium, so it has less chance of harming the child if it goes unstable. Moreover, despite parallel robots generally having small inertia, the Falcon has a higher apparent inertia compared to the Premium. If the user releases the master while it is applying a force on the user’s hand, it will accelerate in free space. This acceleration will be higher for low-inertia master devices (e.g. Premium). High-acceleration impacts of the master on the user’s body can be unsafe. These features point to the Falcon being a better choice for the master.
We are interested in a slave robot with simpler kinematic design letting us better manipulate the objects in the environment. Also, a bigger workspace provides a wider reachable area in the environment; this ensures more flexibility in task development. These imply having a serial robot (i.e., the Premium) as slave. It should be noted that although positional accuracy is generally an advantage of parallel robots, translational position resolution of the Premium (860 dpi) compared to the Falcon’s (400 dpi) indicates the Premium’s higher positional accuracy. This is largely a factor of the difference in cost of the systems. Having fine resolution in the environment could be beneficial in future applications if fine detailed tasks are selected. Machine vision and intelligence can help to guide the slave interface to the correct position. .
We will match the interface for the Falcon (master robot) to each individual’s physical capabilities and interface for the Premium (slave robot) to the proposed tasks. The Falcon’s default interface is a removable spherical grip that can be replaced with a pistol grip designed for gaming, a pen-shaped stylus for virtual computer interaction, or a needle insertion for simulated surgery. The Premium comes with a removable pen-shaped stylus. Other end-effectors are thumb-pad and scissors for surgical training. These interfaces will be used or adapted, or custom ones will be built to replace the commercial ones.
TUNING CONTROL PARAMETERS
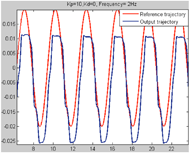
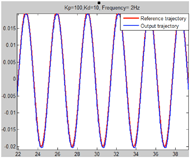
To determine the ideal control parameters for each robot, a proportional-derivative (PD) controller for the master and one for the slave were applied . The parameters were experimentally adjusted and trialed to determine the system’s stability threshold (where the system goes instable) while still ensuring the highest possible transparency (while using the master robot, the user feels as if he/she is directly manipulating the object in the environment) by varying control gains, Kp (proportional gain, N/m) and Kd (derivative gain, N/m).
We first stabilized the Premium (due to its lower apparent inertia and higher risk of instability). To this aim, its movements were observed under different Kp and Kd parameters to tune its controller using a trajectory following method, with a sine-wave as desired trajectory2. The Premium's trajectory best resembled the sine wave with Kp= 70 and Kd= 10. The Premium’s trajectory under untuned and tuned controllers is shown in Figures 2 & 3.
Next, the Falcon’s controller was tuned in a closed-loop PEB control to achieve the best transparency. A marker pen was attached to the Premium robot’s distal link, and the master-slave position tracking performance was experimentally examined in a drawing task under unilateral (without haptic feedback) and bilateral (with haptic feedback) controls (Figures 4a and 4b). The best position tracking performance was obtained under bilateral control with Kp= 350 and Kd= 13. The presence of haptic feedback in the bilateral control mode has led to smoother positions for the slave robot and better drawing task performance.
Discussion and CONCLUSION
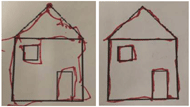
The Novint and Premium were selected as the master and slave robots, respectively, on the basis of general features of parallel and serial robots as well as the system’s proposed application. However, future experiments will establish the reliability and feasibly of these robots with our target users and tasks. There are also some salient points worth mentioning:
- A “fair comparison” of two robots happens if their joints are only prismatic (slide in and out) or rotary (have rotational movement), and they have the same working volume (Briot and Bonev, 2007). Though our robots have only rotary joints, they are varied in their DOFs. This can be neglected since 3-rotational DOFs in the Premium’s interface are attributed to the gimbal attached to its arm and will not be used for our tasks. So, we end up having two 3-DOF robots with only rotary joints and translational DOFs in the task space (Cartesian space). As suggested by Briot and Bonev (2007), the varied workspace can also be compensated for by constraining the robots’ workspaces to an identical geometry and evaluating their performances on a given task.
- The Falcon’s delta joint arrangement (Clavel, 1989) has the advantage of having high operation speed and high positional accuracy (Martin & Hillier, 2009). Yet, it introduces singularities (points where maximum extension and foldback of links occur). The haptic sensations caused by singularities can confound the user’s perception of slave’s interaction forces with the environment.
- Though perceived forces by the Falcon seem sufficiently accurate for our future tasks, gravity compensation and joint friction estimation methods (e.g. Grotjahn) will be applied to increase the transparency.
- The Falcon’s limited workspace will be suitable for users with a limited range of motion. For those with gross hand movements (larger range of motion), we may consider a different robot which provides bigger range of motion.
Future work will be to expand the functionality of system to haptically guided play environments compatible with the children’s abilities. Virtual fixture (software generated forces) will impose virtual constraints on geometry of drawing and painting tasks (to guide the user’s input interface) in virtual and physical environments to investigate the effect of virtual fixture guidance as well as different environments on user performance.
References
Atashzar, S. F., Polushin, I. G., & Patel, R. V. (2012). Networked teleoperation with non-passive environment: Application to tele-rehabilitation. Intelligent Robots and Systems, 5125-5130
Briot, S., & Bonev, I. A. (2007). Are parallel robots more accurate than serial robots?
BS EN ISO 9241-910:2011 ergonomics of human-system interaction. framework for tactile and haptic interaction(2011). BSI Standards Limited.
Chen, X., Ragonesi, C., Galloway, J. C., & Agrawal, S. K. (2011). Training toddlers seated on mobile robots to drive indoors amidst obstacles
Clavel, R. (1990). Device for the movement and positioning of an element in space
Covarrubias, M., Gatti, E., Bordegoni, M., Cugini, U., & Mansutti, A. (2014). Improving manual skills in persons with disabilities (PWD) through a multimodal assistance system. Disability & Rehabilitation: Assistive Technology, 9(4), 335-343. doi:10.3109/17483107.2013.799238
Crespo, L. M., & Reinkensmeyer, D. J. (2008). Haptic guidance can enhance motor learning of a steering task. Journal of Motor Behavior, 40(6), 545-557.
Gibson, E. J. (1988). Exploratory behavior in the development of perceiving, acting, and the acquiring of knowledge. Annual Review of Psychology, 39(1), 1.
Grotjahn, M., Heimann, B., & Abdellatif, H. (2004). Identification of friction and rigid-body dynamics of parallel kinematic structures for model-based control
Hayward, V., Oliver, R. A., Manuel Cruz-Hernandez, Grant, D., & Gabriel Robles-De-La-Torre. (2004). Haptic interfaces and devices. Sensor Review, 24(1), 16.
Lee, L. F., Analysis and Design optimization of in-parallel haptic devices (2010). Department of Mechanical and Aerospace Engineering, State University, New York
Marchal-Crespo, L., Furumasu, J., & Reinkensmeyer, D. J. (2010). A robotic wheelchair trainer: Design overview and a feasibility study. Journal of Neuroengineering and Rehabilitation, 7, 40-40. doi:10.1186/1743-0003-7-40
Martin. S., Hillier, N. (2009). Characterisation of the Novint Falcon Haptic Device for Application as a Robot Manipulator. Robotics and Automation
Minogue, J., & Jones, M. G. (2006). Haptics in education: Exploring an untapped sensory modality American Educational Research Association.
PANDILOV, Z., & DUKOVSKI, V. (2014). Comparison of the characteristics between serial and parallel robots. Acta Technica Corvininesis, 7(1), 143.
Sjostrom, C. (2001). In Salleh S. H., Boashash B. and Boashash B.(Eds.), Designing haptic computer interfaces for blind people Universiti Teknologi.
Tavakoli, M., Patel, R. V., & Moallem, M. (2006). A haptic interface for computer-integrated endoscopic surgery and training. Virtual Reality, (2)
Wavering, A. J. (1999). Parallel kinematic machine research at NIST: Past, present and future. Paper presented at the pp. 17-32.
Acknowledgements
I would like to thank Seyed Farokh Atashzar from University of Western Ontario for his help with the program.