DESIGN AND DEVELOPMENT OF A STEP CLIMBING SEQUENCE FOR A NOVEL ELECTRIC POWERED WHEELCHAIR
Jorge Candiotti BS1, Hongwu Wang PhD1, Cheng-Shiu Chung MS1; Motoki Shino PhD2, Rory Cooper PhD1
1Human Engineering Research Laboratories, Department of Veterans Affairs, Pittsburgh, PA
2School of Engineering, University of Tokyo, Tokyo, Japan
ABSTRACT
Standard Electric Powered Wheelchairs (EPWs) have been unable to overcome architectural barriers such as curbs and steep roads. In the past 20 years many models of EPWs have been designed to climb curbs; however, these models are often larger than standard EPWs that might not meet the user’s needs and not pass the ISO/RESNA standard wheelchair tests. The goal of this project was to develop a novel electric powered wheelchair, called PerMMA2, with the ability to climb steps and drive over challenging surfaces such as cross slopes, and steep hills. Thus, the design of PerMMA2 was developed while taking in consideration the ISO/RESNA standard - for the current EPWs. This paper focuses on the mechanical design of PerMMA2 and a description of one of its applications: step climbing. A kinetics and kinematic model based step climbing sequence was simulated with Open Dynamic Engine software. Simulation results showed that the current design of PerMMA2 could successfully climb up to 20.32 cm curb high. Future work will focus on exploring more tasks with PerMMA2 like lateral pressure relief and maintaining a level seat under uneven surfaces and cross slopes.
KEYWORDS
Climbing wheelchair, Open Dynamic Engine, wheel position, PerMMA2
BACKGROUND
According to the U.S. Census Bureau’s Survey, from 1990 to 2005, the population using wheeled mobility devices (WMDs) increased 4.3% per year, and were about 3.3 million adults using WMDs [1]. EPW use is at an all time high and growing in the United States and estimated 400,000 EPW users by 2010 in United States [1]. However, current mechanical designs and control algorithms of EPWs limit users’ mobility to drive in challenging road conditions such as gravel, grass, cross slope surfaces, and steep hills [3][3]. EPW users also cannot access other areas due to architectural barriers such as curbs and stairs. In some places, the Americans with Disabilities Act Accessibility Guidelines (ADAAG) [4] criteria are not even met.
Several researchers have developed EPWs with the ability to climb steps and successfully have overcome these barriers. Nagasaki University designed an eight wheel wheelchair with an extendable rear arm to reach high steps [5]. A similar concept was used by the Politecnico di Torino which developed a chair that had three wheels in each corner of the base [6]. The University of La Castilla-La Mancha developed a climbing wheelchair which deploys a foot onto the step to push the wheelchair up and drag the casters forward to the next step [7]. The authors might have focused on the climbing process; however, some aspects of their wheelchair design may not pass the ISO/RESNA standard wheelchair tests, particularly Section 5 [8], as result of the large wheelchair dimension, limited turning ratio and driving performance.
The iBOT3000 was a wheelchair with stair/curb climbing ability that is no longer available [9]. The TopChair is a climbing EPW only available in the European market which includes the same features as an EPW with the addition of a track under the base which is activated only during a climbing sequence [10]. This feature makes the wheelchair heavier than standard electric powered wheelchairs.
The primary purpose of this study was the design and development of PerMMA2 as a solution to the above mentioned issues of climbing steps and driving under challenging road conditions while meeting the ISO/RESNA standards. The step in this process was to simulate climbing a standard 8 inches curb high or less.
METHODOLOGY
Mechanical design:
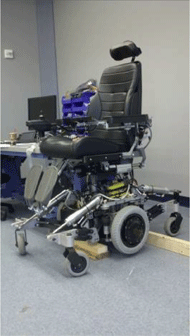
A novel EPW called PerMMA2 is the second generation of a personal mobility and manipulation appliance wheelchair (PerMMA) [11]. The main focus of the PerMMA2 was on the base frame and the development of driving applications. The mechanical design of PerMMA2 (Figure 1) consists of a pneumatic system that controls the height of the four caster wheels and the two driving wheels through the use of pneumatic valves. This system allows the wheels to be positioned within a four inches range in the superior/inferior direction. In addition, an electric actuator, located under the base, allows positioning of the driving wheels along the anterior/posterior axis over eight inches (Table 1) [12]PerMMA2’s dimensions were designed to be similar to those of standard powered wheelchair.
Wheels |
# of Wheels |
Degree of Freedom (Distance) |
---|---|---|
Driving Wheels |
2 |
Vertical Axis (10.16 cm) |
Rotation |
||
Horizontal Axis (20.32 cm) |
||
Rear Casters |
2 |
Vertical Axis (10.16 cm) |
Spinning Rotation |
||
Swivel Rotation |
||
Front Casters |
2 |
Vertical Axis (20.32 cm) |
Spinning Rotation |
||
Swivel Rotation |
The controller was adapted from our previous advanced real-time control platform [3]. In addition to a single board computer, joystick and switches, the controller is also connected to other peripherals such as pressure sensors, linear encoders to determine the position of the wheels, an inertia sensor, and potentiometers to calculate the tilt and recline angles of the chair.
Step Climbing Sequence:
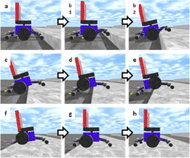
The goal of this study was to develop and model the climbing sequence for a curb height of 20.32 cm (8 inches) or less. The climbing sequence consisted of two steps: A manual step performed by the user and an automatic step performed by the controller. Figure 2 shows the step climbing sequence and described below:
-
First the wheelchair must be in Driving Mode – the wheelchair is in Mid-wheel drive and user controls the driving performance of the wheelchair - the user drives until the front casters contact the curb. This allows the controller to determine the distance between the driving wheels and the curb through the pressure and position sensors. The user then sets PerMMA2 to Climbing Mode. Climbing Mode will start by aligning the wheelchair perpendicular to the curb using the pressure sensors in the front casters. The Driving wheels will be moved forward to be in Front-wheel drive.
-
Next, the wheelchair will be moving at a slow constant speed (1m/s). This action in combine with the elevation of caster wheels is used to measure the curb height. Then, the front casters will elevate to move 8 inches in height (Figure 2.b1). If the height is not reached the rear casters will rise as well to move to the desire height (Figure 2.b2).
-
Then, the front casters will move down once placed in the curb. This action will suspend the driving wheels in air. Next, the driving wheels will move back until it makes contact with ground and drive forward. The purpose of this action is to place the wheelchair base in the curb in order to move the driving wheels in the curb as well in the next step. When the front casters are positioned on the curb, caster brakes are applied to prevent the wheelchair from rolling backwards.
-
Next, the rear casters will be pushed down using the pneumatics system and the driving wheel will be raised up leaving the driving wheel suspended in the air.
-
The driving wheel carriage will be moved forward until the driving wheels are in top of the curb. These will be pushed down until contact is made to the curb
-
Then, the driving wheel carriage will be moved back until the wheelchair base is completely above the curb.
-
Once the driving wheels and front casters are above the top of the curb, the driving wheels will be lowered down to move the rear casters to the curb.
- Finally the wheelchair will drive automatically until all wheels are making contact with the new surface above the curb. After this, the wheelchair will resume to driving mode and user will have control of the wheelchair.
The user will have the option to pause/ resume the climbing sequence or cancel it. When the Climbing mode is cancelled the wheelchair will automatically return to the position before the climbing sequence started.
Kinematic model
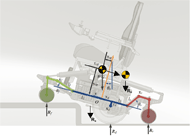
The software Open Dynamic Engine (ODE) was used to simulate the forces and kinematics applied during the climbing sequence and to develop the algorithm for step climbing (Figure 3).
Each step of the climbing sequence was performed based on the position of the center of the driving wheels to the edge of the curb. The initial position of the driving wheels was defined when the front casters reaches the edge of the curb.
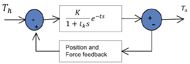
The step climbing sequence simulation was controlled using force control and position feedback. Force control was used to apply the necessary pressure in the air pneumatics to elevate the casters to the required distance. Figure 4 shows the control diagram which regulates the movement of the pneumatics. A Torque Force (Th) is applied to a pneumatic actuator which passes through a proportional constant K and a low pass filter to reduce the pneumatics’ speed and obtain a smoother control. The position of the pneumatic actuator and the force applied to it are calculated and feedback to the system to prevent force overshoots and damage to the system and to optimize the applied torque (Ta) to the pneumatic actuator.
Shift in Center of Mass:
The position of the center of mass (CoM) was calculated to balance the wheelchair and provide safety to the user during the curb climbing step. The optimal location of the CoM was calculated by finding the relationship between the users’ mass and the minimum driving wheel position. A wheelchair’s mass of 136 kg and user weight between 60 - 100 kg was used in the simulation. The initial position of the driving wheels was in mid- position (25.1 cm with respect to the front of the frame). The driving wheels were moved forward 4.3 cm to prevent the wheelchair from leaning forward when the front casters elevate.
The algorithm to shift the center of mass is defined as following: the position of the center of mass (xc) must be located between the driving wheels (x
d) and position of the rear casters (x
r) as shown in equation 1. Also, the force in the rear casters (R
r) and driving wheels (R
d) must be equal to or greater than the total weight of the user (R
u) and base (R
b) (eq. 2). The purpose to locate the center of mass is to balance the wheelchair during the step climbing sequence and prevent unintentional movements in the wheelchair that can be dangerous to the user.
xc ≥xr -xd | (eq.1) |
Rr + Rd – Ru – Rb = 0 | (eq. 2) |
PerMMA2’s dimensions were designed to be similar to those of a standard powered wheelchair as shown in Table 2.
Wheelchair Model | Base Length | Overall Width |
---|---|---|
Permobil C500 | 49.5” | 25.5” |
PerMMA2 | 40” | 26” |
Invacare TDX | 35.25” | 25.5” |
Overall RESNA dimensions [8] | 47.24” | 27.56” |
DISCUSSION
The modeling of the climbing sequence of PerMMA2 can be applied to any curb height of 8 inches or less. This is important as standard curbs height is 8 inches but they tend to decrease due to deterioration.
The ODE software and the Single Board Computer of the PerMMA2 wheelchair use the same programming language, C/C++, which makes the algorithm transition to the wheelchair controller simpler. However, the ODE algorithm needs to be calibrated based on the sensor outputs to provide accurate control of the pneumatic actuators.
The pneumatic actuators on the system of PerMMA2 system may require some modification of the control algorithm. The pneumatic system is a non-linear system as it depends on air valve pressure. This might limit the control when applying pressure to raise the wheels. An alternative system would be to use electric actuators instead of pneumatics since it is a linear system; however, electric actuators consume more battery power, are more expensive and have a slow response.
FUTURE WORK
A future goal is to evaluate the control simulation of the step climbing sequence by applying it to PerMMA2. A secondary goal is to be able to climb three steps to overcome stairs; however, this requires some modification to the current wheelchair.
The ability of lifting up/down each wheel independently allows PerMMA2 to perform other applications such as a lateral pressure relief for people and an automatic seat leveling while driving over uneven surfaces. These applications can be performed manually with the use of switches; however, more work is in progress to perform these applications automatically. The features of PerMMA2 will be used in combination with another project that recognizes different terrains and change acceleration and velocity according to these terrains [4]. The safety of the user is a high priority during the development and simulation of the step climbing.
REFERENCES:
[1] U.S. Access Board Washington, DC (2003). Demographics of Wheeled Mobility Device Users. In Conference on Space Requirements for wheeled mobility. NYC: Buffalo. Available from http://www.ap.buffalo.edu/idea/Anthro/spacerequireme ntsforwheeledmobility.htm.
[2] LaPlante M, & Kaye HS (2010). Demographics and trends in wheeled mobility equipment use and accessibility in the community. Assistive Technology, 22(1): 3-17.
[3] Wang H, Salatin B, Grindle G. G, Ding D, Cooper R. A (2009). Real-time model based electrical powered wheelchair control, Medical Engineering & Physics, Volume 31, Issue 10, December 2009, Pages 1244-1254
[4] ABA Accesibility Guidelines for Buildings and Facilities http://www.access-board.gov/adaag/html/adaag.htm
[5] Lawn M., Ishimatsu T. (2003). Modeling of a Stair-
Climbing Wheelchair Mechanism with High Single-Step Capability. IEEE Trans. On Neural Sys and Rehab
Eng, Vol 11, Issue 3, pp. 323-332.
[6] Quaglia G, Franco W, Oderio R (2009). Wheelchair.q, a mechanical concept for a stair climbing wheelchair. Robotics and Biomimetics (ROBIO) IEEE International Conference, pp. 800-805.
[7] Morales R, Feliu V , Gonzales A, Pintado P . (2006). Kinematic Model of a New Staircase Climbing Wheelchair and its Experimental V alidation. The International Journal of Robotics Research, vol. 25, Issue 9, pp. 825-841.
[8] ISO standards: Wheelchairs – Section 5: Determination of dimensions, mass and maneuvering space ISO 7176- 5
[9] Uustal H, Minkel JL (2004). Study of the independence IBOT 3000 mobility system: An innovative power mobility device, during use in community environments. Archives of physical medicine and rehabilitation, vol. 85, no. 12, pp.2002-2010.
[10] Laffont I, Guillon B, Fermanian C, Pouillot S, Even- Schneider A, Boyer F, Ruquet M, . . . Lofaso F (2008). Evaluation of a Stair-Climbing Power Wheelchair in 25 People With Tetraplegia, Archives of Physical Medicine and Rehabilitation. Volume 89, Issue 10, October 2008, Pages 1958-1964
[11] Xu J, Grindle G.G, Salatin B, Vazquez J.J., Wang H, Ding D, Cooper R.A. (2010). Enhanced bimanual manipulation assistance with the Personal Mobility and Manipulation Appliance (PerMMA). Intelligent Robots and Systems (IROS), 2010 IEEE/RSJ International Conference: 5042-5047
[12] Quality Life Technology (2011). “Design and Development of Adjustable Wheel Positioning for Power Wheelchair Base.” Pittsburgh, PA. Chen-Shiu Chung et al.
ACKNOWLEDGEMENTS
The author would like to acknowledge the shop staff at the Human Engineering Research Laboratories (HERL), Garrett Grindle, Juan Jose Vazquez, Chengshiu Chung, Hongwu Wang and Elaine Houston for their collaboration to complete the second generation of PerMMA. This project was funded by the NSF-ERC Grant #0540865
CONTACT INFORMATION
Jorge Candiotti. BS, University of Pittsburgh, Human Engineering Research Laboratories, Pittsburgh, PA, 15206, EMAIL: jlc118@pitt.edu
PDF Version