MEASUREMENT SYSTEM TO ASSESS THE BIOMECHANICS OF INDEPENDENT CAR TRANSFER AND WHEELCHAIR LOADING
1,2Philip Requejo, PhD; 1Somboon Maneekobkonwong, MSME; 3Carmen Muller-Karger, PhD; 2Puja Ruparel, MSBME; 2Lisa L. Haubert MSPT; 2Sara Mulroy PhD, PT
1Rehabiliation Engineering Program and 2Pathokinesiology Laboratory, Rancho Los Amigos National Rehabilitation Center, Downey, CA, USA
3Department of Mechanical Engineering, Simon Bolivar University, Caracas, Venezuela
INTRODUCTION
The ability to transfer safely to a variety of surfaces is a fundamental requirement of independent mobility for individuals who use a manual wheelchair (WC) and aging with a disability. A consequence of the current near-normal life expectancy for individuals with paraplegia is that the majority will eventually experience significant and function- limiting shoulder pain. The repetitive physical demands of community mobility on the upper extremities for individuals who push a manual WC are not tolerated on a long term basis, often resulting in shoulder pain after as little as 2 years; causing many individuals to lose their physical independence, including those without primary involvement in the upper extremities (1). Thus, shoulder dysfunction and pain can present a functionally significant loss of independence and decreased quality of life for this population (2).
Transportation and the specific ability to drive independently are important determinants of employment status and quality of life for individuals with SCI (3,4). However, independent driving also requires transferring oneself and lifting a WC in and out of the car. Of the tasks examined in a study by Pentland and Twomey (1991), “work and school activities, outdoor wheeling, household work/child care, and loading a wheelchair into a car” were most commonly associated with shoulder pain (5). Furthermore, Curtis et al. (1999) reported that for long-term WC users, the greatest amount of shoulder pain was experienced when the functional activity required extremes of shoulder range of motion, overhead positioning, or a high level of upper extremity strength (6). Since car transfers and WC loading encompass all three of these, it is crucial to identify the specific biomechanical demands at the shoulder in order to identify prevent shoulder pathology and loss of functional independence.
The purpose of this technical paper is to describe the development of a measurement system to assess the biomechanics of independent WC-to-car transfer and lifting of the WC frame into and out of a car. With this system, we aim to evaluate the shoulder joint kinematics and kinetics of these tasks in order to document the mechanical loads experienced by individuals who transfer independently with various techniques from their personal manual WCs to vehicles of different heights. This information is critical to the development of strategies to reduce shoulder demands during task performance and strengthening of critical muscle groups for maintaining independence and long-term community participation.
MATERIALS AND METHODS
Instrumented Car
We instrumented a Toyota Camry (donated by Toyota Motors, Torrance CA) by cutting out the front, rear, roof section, and suspensions. We created a set of instrumented frames using rod end bearings to install 7 mini low profile load cells (300lb, 500lb max MLP Series, Transducer Techniques; Temecula, California); strategically placed to measure 6-degree-of- freedom forces exerted on the steering column, driver seat, and driver’s side overhead grab bar (Figure 1). We built a standing support frame to allow height adjustments for simulating different vehicle heights (e.g. sedan, small SUV, truck). We modified the B-Pillar on the driver side such that the opening of the door can be adjusted to replicate different entry opening space of different vehicles, if necessary.
We used a PC-based (32-Bit Pentium 4 2.66GHz) data collection system (DasyLab 11.0 Software, PD2-MF-64- 400/14L PowerDaq A/D card) to collect all 3 sets of instrumented load cells (21 channels of force load cells).
Motion Capture System
We used a sixteen-camera Optitrack® V100:R2 (Natural Points) motion capture system mounted on a custom-built PVC frame assembly mounted over the instrumented car (Figure 2). We used the coordinates of 19- mm retro-reflective markers to track the motion (AMASS, C-Motion, Inc.) of the test participant, wheelchair frame, and car positions. In order to accurately determine the position of each marker, cameras were placed in an optimal location so that every marker was visible to at least six cameras.
We defined the global coordinate system (GCS) by placing an L- frame of known dimension on the floor of the laboratory. The GCS is an orthogonal right handed coordinate system with X and Y axes as horizontal; X axis pointing perpendicular to the sagittal plane, Y axis pointing towards the driving direction and Z axis as vertical; parallel to the gravitational axis. We recorded the locations of the instrumented load cell frames relative to the GCS in order to determine their positions when the car height is adjusted.
The motion capture data (100 Hz) was simultaneously collected and synchronized with the reaction forces (2000 Hz) via a sync pulse from the AMASS software for each trial and saved onto a hard drive for subsequent processing and analysis.
Kinematic and Kinetic Model
Twenty-seven markers were used to track the motion of the trunk (5 markers) and the bilateral upper limbs (11 markers each) (Figure 3). The trunk markers were: 1st and 4th thoracic spinous (T1and T4), the manubrium (MAN) and the xiphoid processes (XIPH), and the left coracoid process of the scapula. Upper arm motion was tracked using: a greater tubercle marker (TB), medial and lateral elbow epicondyles (markers LEP and MEP), and markers between the proximal and middle1/3 of the posterior lateral humerus and at the middle of the anterior lateral humerus. Forearm markers were place at the junction of the proximal and middle 1/3 of the anterior forearm, the junction of the middle and distal 1/3 of the posterior forearm, and the radial and ulnar styloid processes (RSP and USP). Hand markers were placed on the third and the fifth posterior metacarpal heads (M3 and M5). The wheelchair frame motion was tracked using 9 markers placed strategically around the frame assembly - a known distance from the gravitational center of the frame.
We defined the segments following the description of Rao et al. (7). For each segment an embedded Local Coordinate System (LCS) was defined, with Y’ axis pointing from posterior to anterior and Z’ axis in the vertical direction. The origin of the LCS is located at the proximal end of each segment.
Data Collection, Processing and Analysis
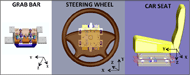
Individuals with ASIA A B or C motor paraplegia who push a manual WC for more than 50% of their mobility participated. They were recruited from outpatient clinics of the rehabilitation center (sample of convenience). All participants were independent drivers and routinely performed the task of self-transfer and loading a WC into their vehicle. Prior to data collection, we provided each participant with a copy of the Bill of Rights of Human Subjects and they read and signed an informed consent form that had been approved by the Institutional Review Board.
A practice session approximately one week prior to laboratory data collection began with participants transferring with their preferred right hand placement into the test vehicle adjusted to their customary vehicle height. If subjects felt they could transfer safely with the alternative hand placements and into the vehicle at the small SUV height, without assistance, these transfers were practiced with stand-by assistance of a physical therapist for safety. A minimum of three trials was performed of each condition. Participants then practiced loading the three different frames into the front passenger and rear seats of the laboratory vehicle during the same session. A minimum of three trials was performed with each frame.
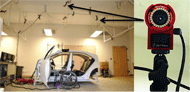
Laboratory testing began with the subjects sitting in their personal WC, ready to lift their body into the car. Subjects were then instructed to place their right hand either on the instrumented seat, grab bar, or steering wheel, to assist in pulling or pushing themselves into the car. Once the transfer was completed, they were asked to place both hands on the steering wheel to indicate that they were finished (Figure 3). After subjects had transferred into the car, they were instructed to lift the WC frame from the ground to the passenger seat or rear seat. The order of hand placement and WC frame placement testing was randomized prior to data collection
The car transfer task was conducted twice; once with the instrumented vehicle set up to simulate the height from ground to the seat of an average sedan (~22”) and again at a height simulating an SUV (~28”). Three wheelchair frames of varying configurations and weights were evaluated; 1) ultra-lightweight L-shaped Ti-lite Ti (3.8kg.), lightweight box frame Quickie GPV (5.9kg.), and lightweight L-shaped Colours Razorblade (4.5kg.). Finally, they were asked to lift the WC frames into and out of the car and placing them on the front passenger seat or rear seat.
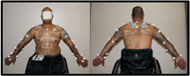
Force and motion data were combined using custom software (C3D Server, MLS, Inc.) and Visual3D (C-Motion Inc., Rockville, MD) was used to implement the three- dimensional model of the upper body and calculate the upper extremity kinematics and kinetics during the transfer and loading tasks. Motion and load-cell trajectory data were smoothed with a 6-Hz and 14-Hz zero-phase fourth-order digital Butterworth low-pass filter, respectively.
Joint kinematics were calculated using an Euler/Cardan rotation sequence with the proximal segment defined as the reference frame (i.e. upper arm relative to torso, etc.). For the lifting trials, the gravitational and inertial forces of the WC frame acting on the upper extremity were calculated from the frame mass and center of gravity linear acceleration, respectively. The shoulder net joint forces and moments during each phase of the transfer and lifting task were determined using inverse dynamics.
RESULTS
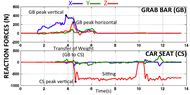
Kinematic and kinetic data from an individual with T12 paraplegia (ASIA A) transferring into the sedan height vehicle and lifting an L-Shaped ultra-lightweight WC frame is presented. This participant scooted forward and placed his right legs into the vehicle prior to transferring into the car. The participant pulled himself into the car using the grab bar with maximum force on his right hand of about 50% of his body weight (400N) (Figure 4) while placing the left hand on the WC wheel and side guard (Figure 5). During the loading task, he folded the seatback prior to initiating the WC frame lift (Figure 6). He lifted the frame from the ground with the left arm in a slight external rotation, while holding onto the steering wheel with the right arm. During placement of the frame onto the rear seat, both hands were used but the right shoulder was in maximum external rotation and abduction; an external rotation moment was observed during this time.
DISCUSSION
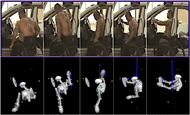
The goal of this project is to maximize independence for aging manual WC users by identifying optimal car transfer and WC loading techniques to preserve safety, independence, and pain-free shoulder function in the home and community. Currently, the measurement system is being used to examine the influences of varying car height, WC frame (weight and dimensions) and right hand placement during car transfer on the upper extremity loads independent transfers and WC frame lifting.
The current investigation documented the extreme position of the shoulder during release of the WC frame into the rear seat; which may predispose the shoulder joint to high stresses that lead to injury. Information from this research is critical to the development of a comprehensive shoulder pain prevention program that is crucial for preserving independence and community participation for individuals with SCI.
CONCLUSION
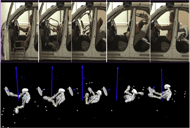
The instrumentation and data acquisition system enables a quantitative biomechanical analysis of the car transfer and WC loading, allowing the evaluation of the demands associated with this high-stress activity that can contribute to the development of shoulder pain and loss of independence.
REFERENCES
- Sie, I.H., et al., Upper extremity pain in the postrehabilitation spinal cord injured patient. (1992) Arch Phys Med Rehabil,. 73(1): p. 44-8.
- Gutierrez, D.D., et al., (2007) The relationship of shoulder pain intensity to quality of life, physical activity, and community participation in persons with paraplegia. J Spinal Cord Med,. 30(3): p. 251-5.
- Kiyono,Y.,Hashizume,C.,Matsui,N.,Ohtsuka,K.,and Takaoka, K. (2001). Car-driving abilities of people with tetraplegia. Arch Phys Med Rehabil 82, 1389-1392.
- Lidal, I.B., Huynh, T.K., and Biering-Sorensen, F. (2007). Return to work following spinal cord injury: a review. Disabil Rehabil 29, 1341-1375.
- Pentland, W.E. and L.T. Twomey. (1991) The weight- bearing upper extremity in women with long term paraplegia.. 29: p. 521-530.
- Curtis, K.A., et al., (1999) Shoulder pain in wheelchair users with tetraplegia and paraplegia. Arch Phys Med Rehabil,. 80(4): p. 453-7.
- Rao, S.S., et al., (1996) Three-dimensional kinematics of wheelchair propulsion. IEEE Trans Rehabil Eng,. 4(3): p. 152-60.
ACKNOWLEDGEMENTS
The contents of this report were developed under a grant from the Department of Education, NIDRR grant number H133E080024. However, those contents do not necessarily represent the policy of the Department of Education, and you should not assume endorsement by the Federal Government.