Dynamic Stability Evaluation Of A Self-Leveling Robotic Wheelchair For Tip Prevention: A Case Study
Courtney Battles1,3, Jorge L. Candiotti1,2, Sivashankar Sivakanthan1,2,Brandon Daveler1,2, and Rory A. Cooper1,2
1Center of Excellence in Wheelchairs and Related Technology, Veterans Affairs Pittsburgh and Human Engineering Research Laboratories (Pittsburgh); 2Department of Rehabilitation Sciences and Technology, University of Pittsburgh; 3Department of Biomedical Engineering, Duquesne University
INTRODUCTION
Electric powered wheelchairs (EPWs) are essential assistive devices for people with disabilities to provide mobility and independent maneuvering within the community [1]. Approximately, 500,000 people currently benefit from using EPWs in the United States (US) alone [2]. However, EPW users often have difficulties navigating in outdoor environments including slopes, uneven surfaces and less accessible areas. Driving over such environments may cause loss of stability in the EPW, leading to accidents [3]. In 2010, a research study reported 100,000 wheelchair accidents in the US, in which 65%-80% were due to tips and falls [4]. Further, Ummat et al showed that of 600 wheelchair users, 57.4%, had completely tipped or fallen from their wheelchair and 16% of these accidents occurred outdoors or on ramps [5]. Falling from a wheelchair can occur in a variety of settings, ranging from transfers, shifts in the center of gravity, wheelchair malfunctions, and environmental factors [6]. Whereas the current EPW technology provides passive suspension to overcome small thresholds and reduce vibration [7], further EPW improvement is necessary to enhance the safety and stability of EPW users when driving inoutdoor environments that do not meet American with disabilities Act (ADA) guidelines [8].
The mobility enhancement robotic wheelchair (MEBot) was developed in an effort to address these issues. MEBot consists of six independently height-adjustable wheels to self-level its seat orientation with respect to the terrain and maintain its center of mass and user within its footprint [9]. Its second iteration provided a larger range of motion in the wheels which allowed its user to manually control the seat orientation when driving up-down and cross-slopes of up to ±20° [10]. To improve MEBot’s functionality, a self-leveling application was developed using the updated MEBot kinematics. The self-leveling application uses an Inertial Measurement Unit (IMU) to measure the pitch and roll angles of the frame relative to a horizontal ground plane. These angles are compared with the seat angles to adjust the wheels’ height and compensate for the angle changes in the terrain.To evaluate MEBot’s self-leveling performance, the paper proposes a dynamic stability evaluation of MEBot compared to a participant’s own EPW when navigating over a controlled driving course. The findings will provide experimental evidence of an advanced robotic EPW to prevent tips/falls when driving in simulated outdoor environments for the safety and mobility enhancement of people with disabilities.
Methods
Participant
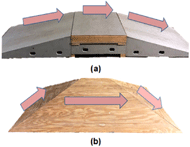
Experimental Set-up
The driving tasks simulated real-world obstacles that EPW users would face in a city or suburban setting outside the home [11]. The first task was a combination of a 10° up-slope, flat platform, and a 10° down-slope (Fig. 1a). The second task was a combination of a curb-cut that had an 18° up-slope, 8° cross-slope, and an 18° down-slope (Fig. 1b).
Protocol
The participant received a demonstration and training of MEBot for 30 minutes until he felt comfortable driving over the driving tasks and received the researcher’s approval. The training included driving in flat and uneven surfaces outside of the controlled environment at his own speed. After training, the participant was instructed to drive over each driving task at a constant speed of 0.5 m/s using MEBot and his own EPW for a total of five trials per driving task. EPW users drive considerably slower than the wheelchair’s maximum speed most of the time [11], commonly at 0.5 m/s.
Data Analysis
The MEBot’s self-leveling application was evaluated in terms of stability because of its relationship with wheelchair tipping [12-14]. Stability was measured by the change in the pitch and roll seat angles in relation to a horizontal surface. During each trial, the pitch and roll seat angles were measured using an IMU sensor secured at the top center of each wheelchair’s frame. Additionally, the response time of the self-leveling application was measured during each trial. The response-time was defined by the required time to bring the wheelchair seat within a ±2.5° threshold. The threshold was determined by common ADA ramps [8] with a safety factor of 2. This study was approved by the Veterans Affairs Institutional Review Board (IRB).
RESULTS
The results showed that the participant’s own EPW recorded similar or higher pitch and roll seat angles to the angles of the driving tasks. In the 10° upward slope, the MEBot’s self-leveling application maintained the seat angle at an average pitch angle of 5.7 ± 0.7°, while the participant’s own EPW maintained the seat at an average pitch angle of 12.9 ± 0.6°. In the 10° downward slope, the MEBot’s self-leveling application maintained an average pitch seat angle of -6.2 ± 0.8˚, while the participant’s own EPW maintained an average pitch seat angle of -14.5 ± 0.8˚ (Table I). However, the self-leveling application was less effective to maintain the roll seat angle within the acceptable angle threshold in comparison to the participant’s own EPW. Except for the curb-cut task, the participant’s own EPW maintained the seat roll angle of the wheelchair within the ±2.5° angle threshold throughout the five trials. However, during the cross-slope of the curb cut driving task, the MEBot maintained a roll seat angle of 5.8 ± 1.0˚, while the subject’s own EPW maintained an average roll seat angle of 8.2 ± 0.2˚ (Table I).
Task | Task Stage | MEBot | Own EPW | ||
---|---|---|---|---|---|
Pitch | Roll | Pitch | Roll | ||
10˚ Task | Up-slope | 5.7 ± 0.7˚ | 1.6 ± 0.6˚ | 12.9 ± 0.6˚ | 0.9 ± 0.3˚ |
Flat | -9.4 ± 0.9˚ | 2.4 ± 1.1˚ | 2.2 ± 0.1˚ | 0.4 ± 0.1˚ | |
Down-slope | -6.2 ± 0.8˚ | 3.7 ± 1.8˚ | -14.5 ± 0.8˚ | 1.3 ± 0.4˚ | |
Curb-cut | Up-slope | 5.6 ± 0.7˚ | 2.8 ± 3.2˚ | 16.1 ± 1.4˚ | 1.4 ± 0.7˚ |
Cross-slope | -8.0 ± 2.3˚ | 5.8 ± 1.0˚ | 0.4 ± 2.6˚ | 8.2 ± 0.2˚ | |
Down-slope | -9.3 ± 1.9˚ | 4.8 ± 2.4˚ | -19.6 ± 0.7˚ | 4.8 ± 2.6˚ |
There was a significant delay when transitioning between angled surfaces using MEBot which caused a spike in the pitch angle; this effect was seen in the transition from the 10° upward slope to flat surface (Fig. 2a) and from the 8°cross-slope to the 18° upward slope (Fig. 2b). Table II shows the average time that MEBot required to self-level in each task. The results showed the time that MEBot required to self-level varied with each trial and with the angle of the slope. The self-leveling application required the longest time to self-adjust in the 10° down-slope task and the cross-slope in the curb-cut tasks with an average of 6.0±4.4 seconds and 7.0 ± 2.1 seconds, respectively.
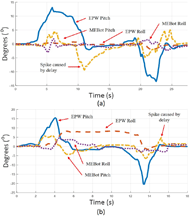
Task |
Task stage |
Response Time (s) |
10˚ |
Up-slope |
2.1 ± 1.4 |
Flat |
5.5 ± 2.7 |
|
Down-slope |
6.0 ± 4.4 |
|
Curb-cut |
Up-slope |
1.9 ± 0.2 |
Cross-slope |
7.0 ± 2.1 |
|
Down-slope |
5.9 ± 1.9 |
DISCUSSION
A previous study showed that the self-leveling application improves the static stability of the MEBot wheelchair [8]; however, further research was required to evaluate its dynamic stability. The results of this study suggested that MEBot reduced the change in the seat angle when driving in simulated outdoor environments compared to participant’s own EPW.
Pitch and Roll Results
Although the self-leveling application was less effective to maintain the roll seat angle within the angle threshold compared to participant’s own EPW, the pitch angle comparison between MEBot and the participant’s own EPW was promising. During the up-slope to cross-slope transition, a spike was shown in the pitch seat angle which showed the limitations of the self-leveling application. First, a limitation in pneumatics lifting capabilities might have caused a delay in the self-leveling performance. The transition between tasks stages shifted the weight towards the front or back of the chair which required higher pneumatics force and time to lift the wheels. Second, pneumatic actuators performance might be limited for quick-changing terrains due to the compressibility of air in its chambers. This compression is potentially significant during transition of slopes to flat surfaces, ultimately manifesting as a negative slope experienced by the user. Additionally, the pneumatic actuators were powered by a high-pressure air tank and dependent by its air volume. Its constant use to self-leveling caused a reduction in its total pressure and its performance. Variability in air consumption with each subsequent trial coupled with a pressure drop over time may explain the required time to self-level.
Whereas MEBot demonstrated good performance in the pitch angle, there were only two instances in which MEBot was able to maintain the roll seat angle near zero in comparison to the participant’s own EPW. For example, during the 18° cross-slope in the curb-cut task, the participant’s own EPW caused him to experience an average roll angle of 8.2 ± 0.2°, while the MEBot self-leveling application demonstrated an average roll angle of 5.8 ± 1.0°. MEBot required longer time to maintain the seat angle leveled than the participant’s own EPW; however, the roll seat angles indicated that MEBot was still effective to level its seat compared to the participant's own EPW when driving in extreme environments or cross-slopes. The variations in the roll seat angle demonstrated by a commercial EPW were caused by a passive suspension system that is more effective in managing small bumps and reducing vibration, but not for larger slopes. Therefore, when traversing cross-slopes, MEBot is more likely to maintain a leveled roll seat angle.
Limitations of the Study
The amount of training with MEBot might have influenced the participant’s normal EPW driving, which can affect the self-leveling reaction time and the change in seat angles experienced in each slope. For example, the participant was told to drive at a constant speed in a straight line over the obstacle, but any deviation from a straight line could introduce undesired pitch and roll angles in a slope that was supposed to have pitch and roll angles of 0.0°. Also, the self-leveling application showed unwanted movements even when MEBot was inactive in a flat surface. This behavior was due to the constant adjustment of the pneumatic actuators. Hydraulic actuators might be a promising alternative to pneumatic actuators due to the incompressibility of hydraulics and ease-of-control. This effect can reduce the unwanted movement and provide a smoother control during the slope transitions. Additionally, the use of a spring and hydraulic actuator in series may reduce the self-leveling actuation to differentially respond to small bumps and angled terrains. This approach may provide a passive suspension similar to commercial EPW and an active suspension to respond to steeper slopes and cross-slopes.
The study was limited to the evaluation of the MEBot’s self-leveling performance in a controlled outdoor environment. Additionally, the study was limited by results obtained from one wheelchair user. Further research should evaluate MEBot in real-world environments and include a higher number of participants with different EPW driving experience and participants’ characteristics to generalize to the entire population. In addition, qualitative measurements should be taken in account to evaluate user’s satisfaction with the technology and experience.
CONCLUSION
The study demonstrated the MEBot’s self-leveling application performance to reduce the change in the pitch and roll seat angles compared to participant’s own EPW in angled slopes. Additionally, the self-leveling application demonstrated its ability to level the roll seat angle within the angle threshold compared to the participant’s own EPW when driving in extreme cross-slopes. However, its limitations must be addressed for further development.
Suspension that is currently found in EPWs is limited to shift its center of mass in uneven terrains with small thresholds, but the EPWs’ stability is questionable in angled terrains that do not meet ADA guidelines [15]. By allowing the wheelchair to automatically adjust its seat orientation when driving in steeper slopes, the wheelchair and user’s center of mass can stay within the footprint of the wheelchair, preventing the user from tipping over or falling. A research study reported that veterans using EPWs highlighted the need for wheelchairs that could automatically adjust or could assist in overcoming obstacles[16]. With increased stability follows increased comfort and confidence to navigate over different environments [6]. The significance of these implications is important to address EPW users’ difficulty to navigate over driving obstacles. With the MEBot’s self-leveling technology, EPW users could be more confident in their abilities to navigate indoor and outdoor environments, ultimately increasing participation and inclusion with others in their communities.
REFERENCES
[1] Edwards, K. and A. Mccluskey, A survey of adult power wheelchair and scooter users. Disability and Rehabilitation: Assistive Technology, 2010. 5(6): p. 411-419.
[2] LaPlante, M.P. and H.S. Kaye, Demographics and trends in wheeled mobility equipment use and accessibility in the community. Assistive Technology®, 2010. 22(1): p. 3-17.
[3] Salatin, B., Electrical Powered Wheelchair Driving Outdoors: The identification of driving obstacles & strategies and the development of an advanced controller. 2011, University of Pittsburgh.
[4] Xiang, H., A. Chany, and G.A. Smith, Wheelchair related injuries treated in USA emergency departments. Injury prevention, 2006. 12(1): p. 8-11.
[5] Ummat, S. and R.L. Kirby, Nonfatal wheelchair-related accidents reported to the National Electronic Injury Surveillance System. American journal of physical medicine & rehabilitation, 1994. 73(3): p. 163-167.
[6] Rice, L.A., C. Ousley, and J.J. Sosnoff, A systematic review of risk factors associated with accidental falls, outcome measures and interventions to manage fall risk in non-ambulatory adults. Disability and rehabilitation, 2015. 37(19): p. 1697-1705.
[7] Ding, D. and R.A. Cooper, Electric powered wheelchairs. Control Systems, IEEE, 2005. 25(2): p. 22-34.
[8] United States, D.o.J., 2010 ADA standards for accessible design. 2010, [Washington, D.C.]: Dept. of Justice.
[9] Candiotti, J., et al., Design and evaluation of a seat orientation controller during uneven terrain driving. Medical engineering & physics, 2016. 38(3): p. 241-247.
[10] Candiotti, J., et al., Kinematics and Stability Analysis of a Novel Power Wheelchair When Traversing Architectural Barriers. Topics in Spinal Cord Injury Rehabilitation, 2017. 23(2): p. 110-119.
[11] Cooper, R.A., et al., Driving characteristics of electric-powered wheelchair users: how far, fast, and often do people drive? Archives of Physical Medicine and Rehabilitation, 2002. 83(2): p. 250-255.
[12] Wang, H., Development and evaluation of an advanced real-time electrical powered wheelchair controller. 2012, University of Pittsburgh.
[13] Thomas, L., J. Borisoff, and C.J. Sparrey, Manual wheelchair downhill stability: an analysis of factors affecting tip probability. Journal of neuroengineering and rehabilitation, 2018. 15(1): p. 95.
[14] ANSI/RESNA, American national standard for wheechairs – Volume 1: requirements and test methods for wheelchairs (including scooters), in Virginia: Rehabilitation Engineering and Assistive Technology Society of North America. 1998.
[15] Bennett, S., et al., Wheelchair accessibility: Descriptive survey of curb ramps in an urban area. Disability and Rehabilitation: Assistive Technology, 2009. 4(1): p. 17-23.
[16] Dicianno, B.E., et al., The Voice of the Consumer: A Survey of Veterans and Other Users of Assistive Technology. Military medicine, 2018.
ACKNOWLEDGEMENT
This work was supported by the VA Center for Excellence for Wheelchairs and Associates Rehabilitation Engineering (Grant B9250-C) and the REU-ASPIRE (Grant 1560174). The authors would like to thank the staff at the Human Engineering Research Laboratories. The contents of this paper do not represent the views of the Department of Veterans Affairs or the United States Government.