Kath M Bogie, D.Phil1,2, Joseph A. Lerchbacker, B.S, 1, Mary Ann Richmond, M.D 1,2, Steven. J. Mitchell OTR/L, ATP1
1Louis Stokes Cleveland VA Medical Center, 2Case Western Reserve University
Cleveland, OH
INTRODUCTION
The overall population at risk for pressure injury development is increasing due to changing demographics. It has been estimated that pressure injury prevention is approximately 2.5 times more economical than treatment [1]. Assistive technology to prevent pressure injury development for at-risk individuals is integral to the goal of providing the highest standards of care The World Health Organization Global Cooperation on Assistive Technology mission states that access to high quality affordable assistive products enables the individual with disability to lead a healthy, productive and dignified life. However, advanced high-performance wheelchair cushions for effective pressure relief are often not available to many users. Even when they are available, many individuals considered to be at mild to moderate risk for tissue breakdown get until they develop pressure injuries.
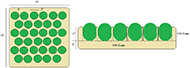
The application of value driven engineering (VdE) principles in the development of assistive technology seeks to provide high performance at greatly reduced cost. High quality affordable wheelchair cushions could provide effective pressure relief for many individuals with limited access to advanced assistive technology.
In response to end user requests, we have developed a modular wheelchair cushion using VdE principles to provide effective personalized high-performance pressure relief at low cost (Figure 1). Preliminary work investigated a range of novel low-cost dynamically responsive materials developed for the non-medical market and which showed potential for use in seating design. A key aspect of the modular cushion's design is its ability to be fitted and customized for each user using a cushion fitting algorithm (CFA). The patented fitting algorithm enables adaption to the individual's unique anatomy and their seating system configuration. Using the CFA, each cushion can be personalized for the user to optimize interface pressure distribution and maintain seated tissue health. The modular array thus optimizes pressure distribution over the cushion surface while the user is sitting providing a high degree of personalization using resilient low-cost materials.
The initial prototypes using gel based inserts were tested under ISO 16480-2 standards against High Profile and Low Profile Roho® and Jay® Medical 2 cushions [2]. Overall the modular cushions performed better than, or on par with, the most widely prescribed commercially available cushions. The thermal conductivity characteristics of these materials also supported a healthy microenvironment with low moisture and temperature levels [3].
The prototype modular cushion was evaluated by using the QUEST 2.0 instrument (or overall appearance, size and dimensions, comfort, safety, stability, ease of adjustment and general ease of use. Weight was deemed an important aspect of wheelchair cushions. Manual wheelchair users would prefer the cushion to be lighter due to the frequent lifting and moving of the cushion. Therapists felt that weight would not be an issue to the user of a power wheelchair. However, it was felt that a lighter cushion would be desirable for manual wheelchair users, particularly when moving the cushion to different support surfaces, for example from a wheelchair to a car seat.
The first generation modular cushion was designed for power wheelchair users. Further development has now been carried out to develop a lighter modular cushion that retains the durability and adaptability of the initial prototype with enhanced suitability for manual wheelchair users.
The SquishINS cushion uses an array of highly deformable, dynamically responsive and lightweight additively manufactured inserts to ensure suitability for manual wheelchair users. The current paper reports on development of the SquishINS inserts together with load testing and a survey of potential end-users.
METHODS
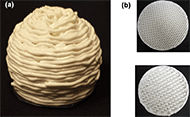
(a) SquishINS with extended base to seat it in the containment layer of the cushion.
(b) Cross-section showing varying inner perfactory structures, which produce different overall stiffnesses.
SquishINS inserts are additively manufactured using modified low cost desktop Lulzbot printers. The 5 classes of SquishINS inserts have varying inner structures which alter stiffness by up to 40%, replicating the variation in the five gel ball classes developed in the initial prototype (Figure 2). In addition to being lighter, the additively manufactured SquishINS can be made with modified surface properties so they 'stick' in the containment layer wells.
Load/displacement compression testing over a force range relevant to seating has been carried out for each class of SquishINS. SquishINS response to loading applied continuously for two hours has been evaluated to determine creep of individual SquishINS under sustained loading. All mechanical testing was done in triplicate for each class of SquishINS.
Systematic testing of full SquishINS cushions has been carried out to ensure that inserts do not fall out under flipping and dropping conditions that are more extreme than would be experienced in regular use. In order to ensure cushion integrity after a fall, an assembled cushion was dropped from a 6ft height, first from a flat, upright orientation and then from a sideways or vertical orientation. After each test, the cushion was examined to see if any SquishINS had fallen out of the containment layer. All tests were performed in triplicate.
Conference attendees at the 2018 PVA Summit were surveyed. Attendees were asked whether they considered it valuable to be able to personalize each user's wheelchair cushion and whether it would be useful to replace only part of a cushion. They were also asked how many people would benefit from a wheelchair cushion developed using VdE principles.
RESULTS
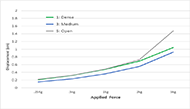
3D printing has created SquishINS that combine lightness and variable stiffness and meet the requirements for durability and adaptability.
Load/displacement testing showed that there was a maximum 7mm compression at the highest load tested for the softest class of SquishINS insert (Figure 4)
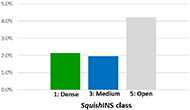
Creep testing showed that after initial compression there was less than 1mm change in SquishINS under sustained loading (Figure 3).
Drop testing showed no SquishINS came out of the containment layer, even under extreme drop conditions. There was minor displacement and some rotation if the cushion landed on angle or on its side. The rotated SquishINS could readily be re-seated without needing to remove the cushion cover.
There was very positive feedback from the 2018 PVA Summit attendees: respondents expressed interest in using a low-cost high performance cushion for themselves or their clients. Personalization of each user's SquishINS cushion and the ability to replace only part of the cushion were considered to be very or extremely useful. It was also considered that many people would benefit from a high-performance wheelchair cushion available at low-cost.
DISCUSSION AND CONCLUSIONS
Many elderly and those with spinal cord injury rely on a wheelchair seating system, made up of a wheelchair and an effective pressure relief cushion. Used together these provide mobility and sitting stability while decreasing skin breakdown risk and increasing overall sitting tolerance. The long-term objective of this project is to develop a range of support surface devices, including wheelchair cushions and mattress overlays that will provide highly cost-effective pressure relief for these individuals at increased risk of tissue breakdown. The modular design concept allows for low-cost customization for individual seating requirements and the capacity for the cushion to be repaired rather than replaced, thus increasing durability.
SquishINS are an innovative concept for modular seating and pressure relief, designed to change shape under seating loads in order to distribute the applied seating forces. SquishINS are manufactured from STL design files which ensure reproducibility across all additive manufacturing systems.
The SquishINS cushion enables low-cost customization and high performance for individual seating requirements. The modular design allows individual SquishINS inserts to be replaced or relocated. Durability is increased because the whole cushion does not need to be replaced. Personalized SquishINS cushions can be created and adjusted using our patented cushion fitting process.
Further development and testing will include comprehensive testing to ISO 16840-2 standards and a clinical pilot study of full-time wheelchair users. Thorough pre-clinical development and user evaluation will provide a strong foundation for translation of personalized low-cost high-performance modular cushions for effective seated pressure redistribution in wheelchair users.
REFERENCES
- Lyder CH, Wang Y, Metersky M, Curry M, Kliman R, Verzier NR, Hunt DR. Hospital-acquired pressure ulcers: results from the national Medicare Patient Safety Monitoring System study. J Am Geriatr Soc 2012; 60:1603–8.
- Freeto T, Cypress A, Amalraj S, Yusufishaq MS, Bogie KM. Development of a Sitting Microenvironment simulator for wheelchair cushion assessment. J Tissue Viability. 2016 Aug;25(3):175-9.
- Freeto T, Mitchell SJ, Bogie KM. Preliminary development of an advanced modular pressure relief cushion: Testing and user evaluation. J Tissue Viability. 2018 Feb;27(1):2-9.