Kimberly Pocwierz, Nicholas Dana, Hassan Hejji, Dr. Andrea Kwaczala
Biomedical Engineering, Western New England University
Introduction:
Nearly 13 million children are affected by inadequate trunk control which is char- acterized by an instability and lack of postural control. This is typically a secondary condition as a result of another diagnosis such as Dystonia, Ataxia, Rett syndrome, spasticity, Wilson's disease, Cerebral Palsy (CP), or Traumatic Brain Injury [1].
In typical development, children build trunk control which starts with the head and neck during early infancy and slowly develops through the spine segmentally, with full pelvic control and the ability to sit upright by 8-10 months. An individual's ability to maintain trunk control can be char- acterized at 7 different levels using a clinical assessment tool called the Segmental Assessment for Trunk Control (SATCo) [2].
In children with reduced trunk control, this can lead to limitations in their ability to sit up and complete motor tasks. These motor tasks such as reach and grasping ability are closely linked with ability to maintain postural control [3], but are also strongly connected with cognitive develop- ment. External trunk support can significantly improve grasping and reaching abilities in develop- ing children [4].
There is a commercially available seating system that is a competitive product, called Firefly GoTo Postural Support Seat. This is a high quality portable and versatile chair that provides lateral sup- port around the waist. It is limited in the level of targeted lateral support and does not provide rigid pelvic control. Additionally, this seat is expensive with a cost of ~$400 in a small, medium and large design implying children will outgrow the seat [5].
The biomedical engineering senior design team at Western New England University was tasked with the development of a seating system to improve trunk control by applying external loads at the appropriate position along the trunk; specifically ensuring proper mechanical stability of the pelvis and controlled placement of lateral supports along the spine. The external support provided by this portable chair may allow people living with mobility limitations to improve upper body function such as reaching and grasping and will improve their interaction with the world around them.
Problem Statement:
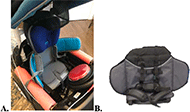
There is a need for an affordable seating system that provides mechanical support through the pelvis, trunk and head in a portable chair design. The design should be uni- versal and allow adjustability as a child grows with removable components to provide the appro- priate level of trunk control to meet each child's unique needs. The chair must provide adjustable lateral support in both breadth, depth and height along the spine and incorporate pelvic nylon straps to control pelvic motion while seated in the chair.
Engineering Design:
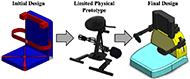
The biomedical engineering design team has utilized the FDA Waterfall design process to develop end user needs, design specifications and generate several design idea- tions. They developed a robust engineered solution to a portable seating system for children. This included several design iterations in SolidWorks 3D software and the construction of a limited functional prototype from recycled wheelchair parts. The final design was selected based on idea- tion of no less than 12 designs that were subjected to a Decision Matrix based on end user needs. Design ideas were combined and the second round of designs were analyzed using a Pugh Matrix which took used design specifications, manufacturability with end user feedback along the way.
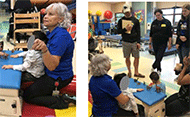
In the research phase of this project, the team was able to reverse engineer a Firefly seating system to understand the benefits and major features of this Benchmark Design. The students were able to observe children utilizing the current gold standard device, and they worked with clinicians to understand the basic requirements to create a portable seat that provided pelvic control. It was identified that the new seat was required to interface safely with other seating systems, such as a GoBabyGo ride-on-car and a Tripp Trapp chair so that it became useful in several at-home appli- cations.
Interdisciplinary Engagement:
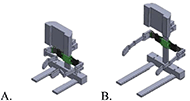
Students developed an understanding of end user needs through conversations with occupational therapists and physical therapists from Shriners Hospitals for Children. A clinical technology specialist, Max Cuppett at Shriners played an instrumental role by providing donated parts from old wheelchairs and offering suggestions on attachment and assem- bly techniques based on his experience building and repairing wheelchairs. Biomedical engineers were able to observe a child being measured using the Sagittal Assessment of Trunk Control to gain better understanding of the targeted level of support required in the design.
Additionally, biomedical engineering students worked with students enrolled in the doctoral oc- cupational therapy program at Western New England University. These doctoral students served as consultants on the project to provide feedback and new perspectives on the design quality and helped provide direction at new phases of the design process. They had a higher level of under- standing for seating systems and wheelchair design to promote comfort and usage by their clients.
A strong understanding of the target population that this device would service, led to better design optimization in the ideation phases of the project. This was critical in the development of a novel and functional final product. Ultimately, to be novel, the design had to apply external loads that could provide the appropriate level of segmental support to the trunk. The lateral stabilizers applied to the trunk needed to be adjustable in girth, depth and slide vertically along the longitudinal axis of the trunk, equating to a 3-axis motion mechanism for the support. Most challenging, the chair needed to accommodate a range of children to expand and contract to hold a 10 month old up to a 4-year old. This helped to reduce the burden of cost for parents and caretakers so only a single seat would be purchased for rapid growth from birth to 5 years of age.
The seating system needed to incorporate pelvic straps that align the pelvis to neutral in a seated position and be adjustable in seated height, seat depth and width to accommodate the age range. SATCo straps would be incorporated into the base of the chair using metal O-rings which would help to loop a nylon seat belt and thigh straps that are connected with plastic clip buckles. Nylon straps are lined with foam padding along the thigh for comfort. These are commonly incorporated into GoBabyGo custom cars at Shriners Hospital so were not a focus for this design project and therefor were not visualized in the design work. The functionality of the strapping system is ex- plained in detail in the work by Rachwani, et. al.
The final design needed to fit into a GoBabyGo ride-on-car or and could easily be attached to a Tripp Trapp chair. The chair would be attached using nylon straps and plastic buckles that are incorporated into the base skeleton legs of the design (not shown) [6]. The most important design feature was the rigid lateral supports which were required to slide up and down the spine to apply appropriate mechanical loads at all the different levels for trunk stability. The new seat also needed to recline so that the back rest could be angled between 90 degrees upright to a recline of at least 120 degrees. By providing these features the seat provides a more universal design to meet the specific mechanical stability needs for a range of ages and children with varying height and seat depth.
Metric | Unit | Benchmark FireFly | Marginal Value | Ideal Value |
---|---|---|---|---|
Cost seat
|
USD
|
400
|
<200
|
<150
|
Age
|
Years
|
3– 8
|
0.83 - 4
|
0.66 - 5
|
Weight
|
kg/lbs
|
30 / 66
|
35 / 77
|
46 / 101
|
Support Levels
|
Thigh Seat belt Lateral Head- rest
|
- √ √ √
|
√ √ - -
|
√ √ √ √
|
Lateral Width
|
mm
|
300
|
300
|
350
|
Seat Height Depth Width
|
mm
|
680 244 300
|
680 <320 <250
|
700 <290 <220
|
This seat was designed to be manufactured as a dissembled kit that comes in a box where end users would assemble and only add the components that are needed to meet their child's unique stability requirements. Design components were modeled off of parts that were used in a wheelchair's ad- justable arm rest. By doing this, the mechanism once used to raise and lower arm rests worked to extend both the height of the seat and the depth of the base. This led to the idea of creating a universal seat skeleton with a consistent part for the spine and the base.
The skeleton frame was covered in a padded seat cushion and a backrest cushion and equipped with a headrest (if necessary) for head control. This universal design allows for similar parts to be assembled with only minimal waste in parts and interchange of small aluminum connector tubes to increase the width of the seat for larger end users. This allowed for the seat to be assembled to meet the child's unique needs while considering design for manufacturability, and provided novel adjustability in seat dimensions. A wide base element was added to connect all components to ensure stability and safety of the chair. The final design focuses on reduced manufacturing costs and minimizes environmental waste in the number of unnecessary components.
Cost Analysis of the Design:
Through the use of low cost aluminum parts that utilize a universal design, the skeleton can be manufactured for a cost <$30. The padding, polypropylene base, and foam can be constructed for $20 per chair and SATCo straps can be added for an additional $10 per seat when purchased at cost from online suppliers. Buying and assembling components in bulk can significantly reduce these costs and materials can be purchased for $39 per unit when at least 30 units are constructed. The seat would be sold to the target market at a cost of $150 which is fair market value for an adaptive seating system that can be utilized for over 3 years. There are funding and marketing opportunities for seating systems of this type where insurance would cover end user costs. Future work could look at reimbursement strategies to ensure our seating design meets the requirements to allow parents to submit for reimbursement through insurance programs. Next steps should also engage in discussions to develop partnerships with Numotion and National Seating and Mobility [7, 8].
Verification and Validation:
The seat underwent verification testing through mathematical and computer simulations. Future validation studies are planned for end user feedback on assembly, ease and timing to seat the child, and the functional improvement in trunk positioning and control through external support provided by the seat. These tests were postponed due to the COVID-19 pandemic. In future work, other biomedical engineering student teams will execute the research plan to fully verify the functionality of the seat.
In the simulation work, testing was conducted to determine safety and comfort of the seat. Finally, a detailed build manual was assembled to ensure the end user had proper access to the configura- tion of the seat, could assemble it easily and that they were aware of the safety precautions when handling and using the seating system.
Future verification tests will include the evaluation of the usefulness of the build manual, study of assembly time, and time to get the child seated properly into the chair. The quantity of applied mechanical load could be characterized using force sensing resistors that can characterize pressure and relative loads across surface along the lateral pads that are interfacing with the body. Design controls were specified using Engineering Specifications.
Compression Simulation for Cushion Design
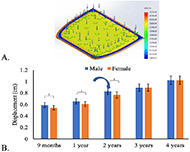
To characterize comfort of the foam used for the seating system, the applied load on the surface of the pad was estimated as the mass from the 50th percentile for both boys and girls from the ages of 9 months up to 4 years of age [9]. A finite element analysis was used to determine the deformation of the custom seat cushion for the seating system. The seat was designed in SolidWorks with dimensions 25.4 x 30.5 x 2.54 cm and made out of a polyfoam block with two 5.08 x 17.8 cm fillets on the front corners of the cushion. In this finite element load simulation, the bottom of the cushion was fixed in all directions and a force was applied downward on the top surface to characterize total displacement. A Two-Sample Student's T-test compared differences in cushion displacement for boys and girls of the same age group. A p-value of less than 0.05 was considered significant.
A 9-month old child in the 50th percentile would displace a polyfoam seat by 0.6 cm (male) or 0.54 cm (female) which represents ~21% of total height of the foam. This increased linearly with age, where finally at 4 years old, the 50th percentile child displaced the seat by 1.0 cm which represents 40% of the total height of the foam consistent in both males and female but still within a comfort zone for foam compression (Two-Sample Student's T-test, *p<0.05).
Safety Tipping Simulation for Seat Stability
To characterize the safety of the device in terms of stability when the child is seated in the chair, a mathematical analysis of the required forces to cause anterior-posterior tipping. The right stable frame and use of safety straps can protect users from falls and injuries [10]. Forms of support include straps, belts, harnesses, and positioning blocks [11, 12].
To determine the stability of the design, a moment calculation was used to determine when tipping would occur. The Center of Mass (COM) and moment equations were used:
Center of Mass =W∗X | Eq. 1 |
Eq. 2 |
W is the Force of the specified object and X is the distance from the point of rotation. Point load locations were derived from anthropometric tables [13,14]. Measured in centimeters, with acro- nyms described: HAT: head, arms and trunk, Uppleg: upper leg, or thigh. The unknown force was derived. The data was derived for cases for the 5th percentile for a 10-month-old female with a height of 66 cm and weight of 6.6 kg and the 95th percentile male whose height was 109 cm and weight is 20 kg to represent the large range of end users [9]. A 10% applied load safety factor was incorporated for the analysis. The seat was then characterized for force generations that were consistent with spastic arm reaches using data published on force generation of spastic CP subjects [15].
The threshold for stability was to withstand greater than a 23 N applied load at the headrest, with- out secondary restraints, that would not cause tipping. The stability testing determined that the large configuration could withstand the required applied force and maintain upright position. However, the small chair's maximum applied peak force was only 16 N that would cause tipping. Since smaller children will not likely generate the same magnitude of forces as larger children, but requires further testing and simulations to better validate the design.
Significance:
This project aimed to develop a seating system to provide targeted trunk control to children with mobility limitations. The team has implemented a functional, universal design that provides individual targeted mechanical support for external trunk control. The use of a universal bracket and mechanical stabilizing bar is novel in its application. This could make the system a stand-alone product or a device that could be modified and interface with commercially available physical therapy tools. This provides a greater level of accessibility to the design which can help improve distribution and use, while also considering the impact of its efficacy as a postural support tool.
The next phases of this project will look to validate the functionality through clinical studies on patients who require different levels of sagittal trunk support. Further work is required to determine end user testing on ease of use, timing studies and surveys to improve the functionality of the application and the manual to assemble the device appropriately. Finally, clinical testing should be used to validate the functionality of the applied mechanical loads at the appropriate SATCo level, and its effects on human performance. This would require Institutional Review Board (IRB) approval, which would likely run through the clinical partners at Shriner's Hospitals for Children.
In conclusion, the implementation of adjustable lateral supports that can apply appropriate me- chanical load at the proper location along the trunk provides the appropriate mechanical stability that will allow children to freely sit upright. This has the potential to improve reach and grasp and help children with disabilities engage in the world around them. Implementation into GoBabyGo cars and equipment intended to improve access to mobility will help these children engage with society and can have major impacts on their quality of life.
References:
- Saavedra, S., Woollacott, M. & van Donkelaar, P. Head stability during quiet sitting in children with cerebral palsy: effect of vision and trunk support. Exp Brain Res 201, 13–23 (2010).
- Butler P.B., Saavedra S., Sofranac M., Jarvis S.E., Woollacott M.H. "Refinement, reliability, and validity of the segmental assessment of trunk control." Physical Therapy, 22(3), 2010.
- Pin T.W., Butler P.B., Cheung H-M, Lai-Fong Shum S. L-F, "Relationship between segmental trunk control and gross motor development in typically developing infants aged from 4 to 12 months: a pilot study" BMC Pe- diatrics volume 19, Article number: 425, 2019.
- Rachwani. The development of trunk conrol and its relation to reaching in infancy: a longitudinal study. (2015).
- Firefly GoTo Postural Support Seat. https://www.fireflyfriends.com/us/goto-seat.
- Liquori B.L., Santana, Y., Brown M.B., Kwaczala, A.T., Gannotti, M. "The Effectiveness of a Service Deliv- ery Model in a Hospital Setting for Use of Ride on Cars by Infants and Children" APPTAC, Nov. 2019.
- Numotion Wheelchair and Mobility Equipment Company. Numotion.com, 2020.
- National Seating & Mobility, NSM-seating.com, 2020.
- Center for Disease Control and Prevention, "National Center for Growth Statistics: Clinical Growth Charts" June 16, 2017.
- Lumley M.A, "Child Restraint Tether Straps -A Simple Method of Increasing Safety for Children" Journal of Passenger Cars: Part 2, 106:3481-3493,1997.
- Bowman J.A, Sanson-Fisher R.W., Webb G.R."Interventions in Preschools to Increase the Use of Safety Re- straints by Preschool Children" Pediatrics, 79(1) 103-109, January 1987.
- Babinec M., Cole E., Crane B., Dahling S., Freney D., Jungbluth-Jermyn B., Lange M.L., Pau-Lee Y.Y., Olson D.N., Pedersen J., Potter C., Savage D., Shea M. "The Rehabilitation Engineering and Assistive Technology Society of North America (RESNA) Position on the Application of Wheelchairs, Seating Systems, and Second- ary Supports for Positioning Versus Restraint." Assist Technol. 27(4):263-71, 2015.
- Drillis, R., and Contini, R. "Body Segment Parameters." Office of Vocational Rehabilitation, HEW Publication. Report 1166–03, 1966:
- Hyncik, L., Novacek, V., Blana, P. "On Scaling of Human Body Models" Appl. And Com. Mechanics. 2007.
- Elvrum A.K., Brændvik S.M., Sæther R., Lamvik T., Vereijken B., Roeleveld K. "Effectiveness of resistance training in combination with botulinum toxin-A on hand and arm use in children with cerebral palsy: a pre- post intervention study." BMC Pediatrics, 2012.
Acknowledgements:
This work was supported by funds from WNEU's Provost Faculty Devel- opment Grant. We are grateful for donations from Shriners Hospital for Children of Springfield, MA of recycled wheelchair parts to make the physical prototype. Most importantly we are grateful for the considerable time invested by our clinical partners with very special thanks for the technical support from Maxwell Cuppett, Yvette Santana, Mary Ellen Brown and Brianna Liquori.