Development Of An Elbow Orthotic With Elastic Elements
Mikhail A. Golovin1,2, Nikita S. Kornilev3
1Institute of prosthetics and orthotics Federal State Budgetary Institution “Federal Scientific Center of Rehabilitation of the Disabled n. a. G.A. Albreht” of the Ministry of Labor and Social Protection of Russian Federation St. Petersburg, Russia (Saint-Petersburg, Russia)
2School of Automation and Robotics , Peter the Great St.Petersburg Polytechnic University (SPbPU), (Saint-Petersburg, Russia)
3Institute of Biomedical Systems and Biotechnologies, Peter the Great St.Petersburg Polytechnic University (SPbPU) (Saint-Petersburg, Russia)
INTRODUCTION
Diseases and injuries of the peripheral nervous system of the upper extremities lead to a significant decrease in living standards, and sometimes to a complete limitation of self-care. The issue of patients with peripheral nervous system disorders leading to functional disorders rehabilitation has become increasingly acute in recent years in the framework of medical and medical-technical conferences and in the literature. Such patients need medical rehabilitation, including using orthoses. An orthosis is an external device used to change the structural and functional characteristics of the neuromuscular and skeletal systems [1]. In this case, the orthosis can be adaptive. It can provide compensation for the weight of a part of the body and dynamically change the auxiliary forces [2].
ACTUALITY
The range of diseases that lead to functional disorders of the elbow joint is quite wide. It includes: acute cerebrovascular accident, complicated injuries of the cervical spine, injuries of the nerves of the brachial plexus, neuromuscular atrophy, the consequences of infectious diseases of the spinal cord. We identified 26 people (14 men and 12 women) with paresis of the upper limb with the inability to perform active movements in the elbow joint among patients who applied to the medical-technical commission of the Federal State Budget Scientific Research Center named after G.A. Albreht in the period from January to October 2019. It was one teenager of 15 years old, the rest were between the ages from 19 to 46. A brachial plexus injury was the most common cause of paresis (10 people) including Erb's obstetric paralysis in two patients. Trauma to the cervical spine was in second place frequency. Four people suffered from neuromuscular atrophy. Two people suffered from myelopathy of the cervical spinal cord and one patient had paresis of the upper extremity amid acute cerebral circulation. Existing types of orthoses are not always suitable for rehabilitation in these diseases and have their drawbacks. A patent search was conducted during the research process. Two conditional groups were established as a result. The first group, orthoses with external energy [4] which used with a complete loss of joint function. And the second group, orthoses consisting entirely or partially of elastic elements [3], which used for injuries of peripheral nerve and partial lost joint functions. The large weight and increased energy consumption are disadvantages of the first group. The second group does not allow the patient to accurately set the value of the auxiliary force. Moreover, these approaches to the development of orthoses - the use of elastic elements and drives with an external energy source - can be combined. This will allow to increase the rehabilitation effect and increase the effectiveness of medical rehabilitation.
To create a prototype of adaptive orthosis the aim of the work was the aim of the work.
RESULTS
An orthosis was created in the process of work. It is consisting of forearm and shoulder sockets made on a 3D-printer, two drives with translational displacement units, an electric drive control module, elastic elements and an orthosis power module.
The prototype of the orthosis consists of two receptacle sockets located above and below the elbow joint and respectively covering the patient’s shoulder and forearm.
Sockets which holding an orthosis on a limb was modeled in Fusion 360, Autodesk Inc., USA. Further, these parts were 3D printed made of PETG plastic, which is suitable for creating functional layouts. PETG plastic is non-toxic and is used to create individual sockets based on three-dimensional models of patient limbs.
A frame made of aluminum parts is mounted on the forearm socket and supports electric drives. Elastic elements are fixed at two points at the orthosis. The upper attachment point is fixed on the shoulder socket. The lower mounting point is mounted on the drive frame. It has one degree of freedom and can move back and forth in the sagittal plane. This movement is carried out by a screw-nut pair, mounted on the output shaft of the electric drive. Elastic elements form a pulley through a rotational connection of sockets.
A system of elastic elements combined with feedback allows you to precisely control the amount of developed auxiliary effort.
The advantage of this design is as follows. If it is necessary to change the auxiliary force the user should not change the number of elastic elements. The electric drives move the lower fixing points. This changes the length of the shoulder of the elastic element. The auxiliary force varies as a result.
DC motors selected as electric drives. A linear potentiometer is located on each drive. It allows to organize position feedback and observe the change in shoulder length.
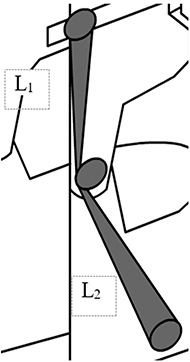
The forces developed during elastic elements stretching were measured to determine the required number of them. In this case, the value of length L1 and the loading arm length L2 were varied (Figure 1).
The analysis of measurements allows to draw the following conclusions. With an increase in L1 an increase in the developed effort occurs. In this case, an overstretching of the elastic element may occur which will lead to decrease the effort. A characteristic feature is the nonlinear increase in load which can be caused by a small sample. It was found that the maximum force of one elastic element is achieved with a termination value of 100 mm and a tension of 130 mm. The developed force does not change with further stretching.
Control system
The control system is based on the esp8266 microcontroller with firmware such as NodeMcu which is able to connect to a Wi-Fi network. The controller program provides the launch of the web server in when turned on. Feedback is implemented through "get" requests that the microcontroller receives from a mobile device. In the process of adaptation, the controller supplies a PWM signal to the driver (L293D) of the DC motors as well as two logical signals: for setting the speed and direction of rotation of the electric drives. Feedback implemented using linear potentiometers. In the process of moving the fastening point, the signal from the potentiometer enters the multiplexer which allows one to register information from the potentiometers in turn on the only corresponding port of the microcontroller used. After that, the recorded stress values are converted into percentages to facilitate adjustment of the adaptation of the orthosis.
Programming took place in the Arduino IDE, which required the installation of additional drivers and libraries. Testing network capabilities was carried out by connecting to a closed local network. The access point was a mobile phone. Despite the possibilities that the use of a microcontroller adds to the project, the board itself has drawbacks. Namely: esp8266 which is the basis of the used board runs on 3.3V logic unlike, for example, Arduino Uno which runs on 5V. This can create conflicts between different elements of the circuit, but this was taken into account in this project. In addition, the microcontroller used has only one analog input / output port. To organize the normal operation of the designed circuit it is needed at least two, since two potentiometers are used to measure. This problem was resolved by adding the CD74HC4051 multiplexer.
The CD74HC4051 multiplexer has eight channels and is also able to work on 3.3V logic. When a binary number system is fed to its control pins, it switches one of eight inputs / outputs to the analog port, which allows to process several analog signals at once. The CD74HC4051 was soldered to a printed breadboard along with the rest of the parts.
Adaptation regulation
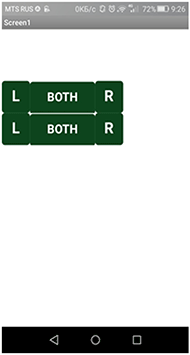
It was necessary to organize convenient control after the orthosis was able to transmit and receive data via wi-fi. To do this, the MIT App Inventor web platform was used to develop a smartphone application. As a result, with the help of the created application, it became possible to start electric drives both individually and together - only setting the direction of movement. The operator gets the opportunity to control both each electric drive individually and both at once.
When it is turned on, the esp8266 controller connects to the specified network and a web server is created on it. There are multiple pages on this server. When requesting the transition to these pages, a direction of movement of the electric drives is changing. An application downloaded to a mobile phone located on the same local network. App calls up the specified pages - thereby controlling the electric drives when the user press the buttons (Figure 2). For example, when entering the page “http://192.168.43.230/FL”, (where 192.168.43.230 is the IP address of the web server specified in the code), two logical and one PWM signal are sent to the left side of L293D. Next, the driver redistributes the power supply to the drive so that it rotates in one direction at maximum speed. When the user release the buttons the page responsible for stopping a particular drive is called up. Also, the controller takes turns reading from two potentiometers with using a multiplexer. The resulting values are converted to percentages of the total movement.
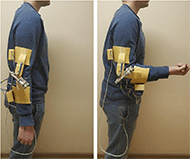
The electric drives and the controller are powered from one battery pack consisting of four 18650 Li-ion batteries with a voltage of 3.7V each through two separate step-down converters: 5V and 12V - to power the controller and power section, respectively (Figure 3).
CONCLUSION
A prototype of the orthosis with the main nodes was created as a result of the work done (Figure 6). The developed device eliminates the disadvantages of existing by combining approaches to their design. Further research will evaluate the prospects of the proposed design in medical rehabilitation.
REFERENCES
- GOST R ISO 8549-1-2011 Protezirovanie i ortezirovanie. — M.: Standartinform, 2013.
- Ponomarenko G.N., Reabilitaciya invalidov : nacional'noe rukovodstvo [Elektronnyj resurs] / pod red. G. N. Ponomarenko - M. : GEOTAR-Media, 2018.
Acknowledgment
We express our gratitude to the heads of Albrecht Federal Scientific Centre of Rehabilitation of the Disabled for the opportunity to conduct this study.